Building Air Tightness Testing: Types and Benefits
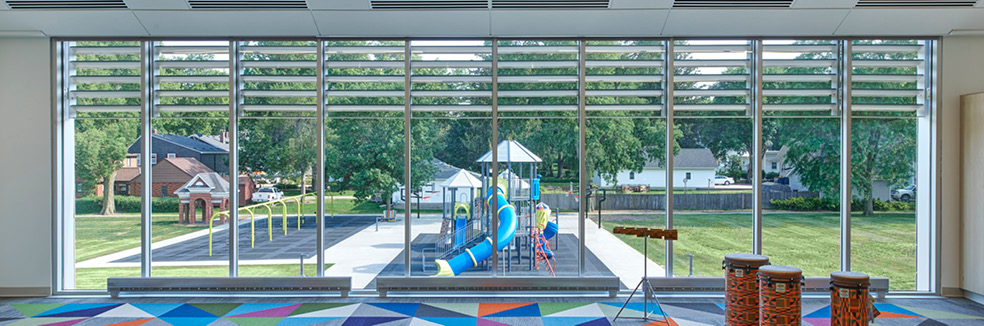
Successful building projects depend, in part, on rigorous testing and inspections. During construction, your project will pause for several tests. Some, like concrete testing, are required by code, while others are optional.
One optional test is building air tightness testing. Also known as air leakage testing, air tightness testing measures how much air is lost through the building envelope. We have helped many clients procure this service and have seen its impact on energy costs and occupant comfort.
This article will explain the importance of air tightness testing, how it works, and whether it’s necessary for your project—helping you determine your needs.
What is Building Air Tightness Testing?
Air tightness testing measures how much air your building loses through its envelope. Cracks and gaps in windows, doors, and cladding can cause leakage, leading to uncomfortable drafts, condensation problems, and increased energy costs.
These problems become more pronounced in the winter. Many homes and commercial buildings utilize a mechanical ventilation heat recovery system which draws in fresh air and extracts heat from the outgoing air. These systems provide necessary ventilation while reducing the energy it takes to heat incoming air.
When a building loses heat through gaps and cracks in the envelope, heat recovery systems cannot operate as efficiently. By testing the building envelope during construction, the contractor can address problem areas and minimize air losses.
How Does Air Tightness Testing Work?
Air tightness testing usually starts with a blower door test. A blower door is a powerful fan that is temporarily mounted to an exterior doorway’s frame. The fan pulls air out of the building to lower the internal air pressure, and higher-pressure air flows out through any gaps or cracks. If the fan is calibrated, the analyst can quantify the amount of air leaving the building.
Although blower door testing helps you quantify the amount of leakage, it does not tell you where leaks occur. Instead, a professional will troubleshoot common problem areas and find leaks.
One common method for finding leaks is theatrical smoke or fog testing. While the blower door is running, the professional will run a theatrical fog machine and watch where fog escapes.
When Should Testing Occur?
In our experience, air tightness testing is most effective when it includes a mid-construction test after the building is enclosed. Although the test can impact your timeline, it allows the construction team to fix air leaks before they get further along in the process.
The final test occurs when the building is complete, and it verifies that you have met your air-tightness goals. If leaks are found during the final test, addressing them can be more expensive and time-consuming. As such, it is important to test the building during construction when leaks are easier to address.
Do You Need Air Tightness Testing?
Air tightness testing is not required by code, but it benefits nearly every project. Reducing air leaks can improve thermal comfort and make your building more energy efficient, reducing costs and carbon emissions. However, some building types benefit more than others.
Residential properties, including multifamily housing, and large buildings like hospitals and schools benefit the most. In these building types, thermal comfort and air circulation are top priorities.
The benefits of testing may not be as noticeable in other building types. For example, a small commercial building with plenty of foot traffic may not receive the same benefits from testing as a larger building type. If the door is constantly opening, the building continuously loses air.
Ready to Learn More?
Every building project involves some degree of testing. While air tightness testing is not required by code, it offers many benefits. By testing the building during construction, you can find air leaks, improve thermal comfort, and reduce energy costs—especially during the winter.
This testing is most effective for residential and large-scale buildings where occupant comfort is a top priority, such as hospitals and schools. To get the most out of the test, we recommend testing midway through construction to allow the contractor to address problem areas.
In addition to air tightness testing, your project may involve mechanical and electrical
commissioning. To prepare, read about what you can expect from the commissioning process.