A standard brick and mortar building was once the only option for new construction. Today, the market has expanded to offer lower-cost alternatives. If you’re operating on a tight budget, you may be considering a pre-engineered metal building.
Pre-engineered buildings refer to steel structural systems that are designed by a manufacturer to handle specific load requirements. The components are produced in a factory and shipped to the construction site.
Although these buildings are traditionally used for agricultural and storage purposes, the market has expanded. The pre-engineering process has been applied to many building types, including athletic facilities and houses of worship.
While pre-engineered metal buildings work well in some situations, they may not fit everyone’s needs. This article will discuss the pros and cons of pre-engineered buildings, helping you determine if you should go down this route or opt for standard construction.
Pros of Pre-Engineered Metal Buildings
Lower initial costs are one of the biggest benefits of pre-engineered metal buildings. The pre-engineered approach simplifies the design process, potentially reducing costs. Additionally, a construction team can quickly assemble the structure after delivery, providing a quicker project turnaround.
If reducing initial costs are your top priority, a pre-engineered building can be a good fit.
These structures are most cost-effective when you need an open space and have low occupancy requirements. They work well for warehousing, storage, and some athletic facilities.
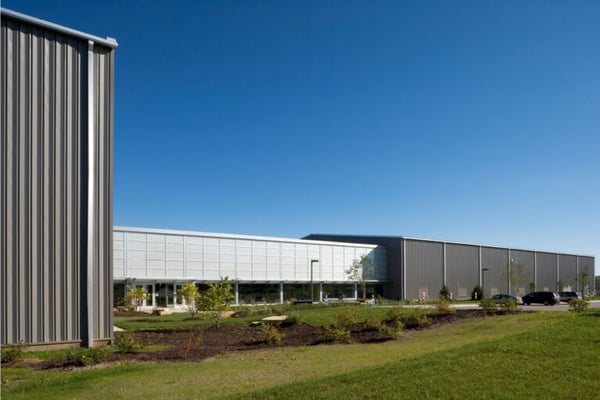
Pre-engineered metal buildings work well for some athletic facilities, like a tennis complex.
Cons of Pre-Engineered Metal Buildings
Pre-engineered metal buildings do not fit every situation. Depending on your goals, standard construction may be more cost-effective both initially and in the long run.
Modifications
While pre-engineered buildings may have a low initial cost, modifying the structure can be expensive. These structures are designed to support specific load requirements, making modifications more complex.
For example, adding components that were not initially planned can be problematic if the original structure cannot support the load requirements. You should plan current load requirements and consider future load requirements to avoid costly modifications.
Additionally, cost-effective pre-engineered buildings have more movement than standard construction, limiting your facade treatment options. The structure’s inherent flexibility makes it difficult to incorporate brick or rain screen systems. If you desire these facade elements, you will need to stiffen the frame, potentially increasing initial construction costs.
The time and cost of these modifications may make standard construction a more straightforward and cost-effective option.
Less Adaptable
Over time, your needs may change, and you may want to expand your facility. Pre-engineered buildings are easy to expand in a longitudinal direction. You simply add more bays.
Upward or adjacent expansions may be more difficult. The frame may not be able to support extra loads, and you may need to strengthen or stiffen the structure.
Future additions may require fire-rated walls, which can be hard to achieve in a lightweight steel assembly. Standard construction is often more adaptable to changing needs.
(Potentially) Higher Life Cycle Costs
Pre-engineered metal buildings may also come with higher life cycle costs. As the structure ages, you may experience problems with condensation and corrosion.
Often, pre-engineered buildings utilize a specific insulation system. Gaps in the insulation can lead to condensation when there are differences between interior and exterior temperatures.
Additionally, thermal bridging can impact occupant comfort, and you may need to scale up your mechanical system to compensate. Standard construction may work better for facilities with strict temperature control requirements.
At the same time, these buildings usually utilize a metal cladding system. Over time, you may experience aesthetic issues with dents and fading.
Although pre-engineered buildings provide a low initial cost, you may pay more long-term maintenance and operational costs than you would otherwise.
Explore Your Options
At the start of a building project, you will encounter options beyond typical standard construction. Pre-engineered metal buildings offer a low initial cost, making them an attractive option for those operating on a tight budget.
However, these structures can be hard to modify and may present higher long-term costs for certain building types.
When exploring your options, carefully consider both initial and long-term costs. Construction costs are only a small percentage of the total cost of building ownership, so plan with longevity in mind. Learn more by reading about the long-term costs to consider when starting a building project.