How to Reduce the Total Cost of Building Ownership
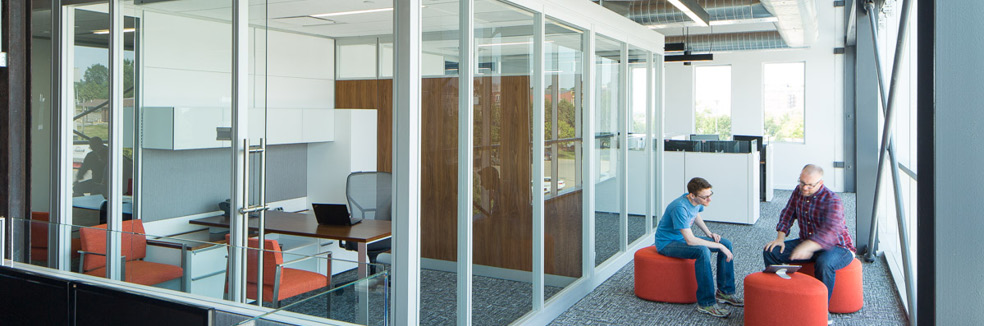
Cost is the driving factor behind many design decisions. After all, a building is a significant investment, and no owner has an endless budget.
Although initial costs are a primary concern during the design process, it is also important to consider the total cost of building ownership. Over 30 years, the cost of maintaining and operating a facility far exceeds the cost of construction.
The design process is an opportunity to lower your long-term expenses. Strategically investing in energy-efficient systems, durable materials, and strategies that improve occupant well-being leads to measurable returns.
This article will prepare you for the design process by discussing how to reduce the most significant categories of cost owners encounter—maintenance and personnel.
Understanding the Total Cost of Building Ownership
Before discussing how to reduce maintenance and personnel costs, let’s put the total cost of building ownership into perspective. One of the best sources for understanding the cost of ownership is a federal government study that examines the costs owners encounter in 30 years.
According to the study, initial costs—including the cost of design and construction—only account for 2% of an owner’s total spending over 30 years. While these costs are often an owner’s greatest concern, they are only a fraction of their longer-term budget.
Maintenance costs—including the cost of maintaining and replacing systems and materials—make up 6%. While these costs should be a prime consideration during the design process, they remain significantly lower than personnel costs.
These costs, making up 92% of an owner’s spending, include employees’ salaries and benefits. Often, commercial owners, schools, and universities are responsible for developing and maintaining their buildings, as well as hiring and retaining staff.
For these owners, the decisions made during the design process can significantly impact their ability to attract and retain talent.
Reducing Maintenance Costs
Reducing maintenance costs starts with a life-cycle cost analysis, a method for assessing the total cost of a building system over its lifetime. Typically performed by a third-party energy consultant, the analysis determines the cost of acquiring, owning, maintaining, and disposing of a system.
Publicly funded projects, like schools and government buildings, must undergo a life-cycle cost analysis for systems that impact performance, including:
- Mechanical systems
- Lighting systems
- Building thermal envelope systems
- On-site electrical generation systems, like photovoltaic arrays
However, an analysis can be done on any project type. Your architect and energy consultant should provide recommendations and help you select the most efficient option.
A life-cycle cost analysis can also help with material selection. A building material with high maintenance and replacement costs will cost an owner more than a more durable option with a higher upfront price.
For example, a material like Vinyl Composite Tile needs frequent waxing and restriping and should be replaced every ten years. Polished concrete, on the other hand, is low-maintenance and can last decades. Although polished concrete costs more upfront, it saves the owner in the long run. Learn more by reading about the life-cycle cost of interior materials.
Generally, we recommend natural materials like wood and steel. These materials are more durable and low maintenance than synthetic options.
Naturally aging materials like Corten steel are lower maintenance.
They also tend to age well. Wood naturally grays, and Corten Steel develops a patina. Occupants can appreciate the building throughout its lifetime and the beauty of its subtle changes.
Natural materials also tend to have a timeless quality, and owners are less likely to make changes to keep the building looking up to date.
Reducing Personnel Costs
Salaries and benefits consume most of an organization’s operating budget. As such, owners are likely to see a return on investment by improving indoor environmental quality and occupant well-being.
A well-designed environment can lead to improved productivity, fewer sick days, and employee retention. Strategies differ depending on the organization and its goals, but there are a few general rules.
First, occupants should have enough space to perform their intended activities. Although smaller floor plates lower construction costs, they can inhibit productivity and lead to long-term losses.
Taller ceiling heights can also create a perception of spaciousness. Occupants are likely to feel more free, creative, and productive when the ceiling does not inhibit their field of view.
At the same time, owners will likely see increased productivity by improving daylighting. A survey published in the Harvard Business Review shows that access to natural light is the top attribute workers want in an office environment.
Ample room and natural light can boost productivity.
Natural light can also improve circadian rhythms, boost energy levels, and improve occupant well-being. Naturally lit workplaces that offer views of the outdoors experience decreased absenteeism.
Daylighting and views play into biophilia—our innate desire to be in and around nature. Materials like wood and stone can remind occupants of nature and even improve air quality, since natural materials are less likely to produce chemical off-gassing than synthetic options.
Natural materials and biophilic design elements can improve well-being.
Above all, we recommend engaging occupants in the early stages of the design process. Your design team should have a thorough understanding of their needs and provide a customized solution. Creating a space where occupants can thrive is the best way to lower long-term personnel expenses.
Prepare for the Design Process
While managing your initial budget, remember to consider the total cost of building ownership. A balanced approach that factors in maintenance and personnel costs is the best way to receive a return on investment.
To lower maintenance costs, ask for a life-cycle cost analysis during the design process. Ask your design team about maintenance and how often you should replace a material or system.
For personnel costs, the best approach is to engage occupants and determine what they desire in the space. Early engagement not only lowers long-term costs but also helps establish clear project goals that steer design decisions.
In our experience, the earliest design phases present the greatest opportunity to influence project outcomes. Learn more by reading how the 80/20 rule applies to the design process.