Life-Cycle Costs for Interior Materials
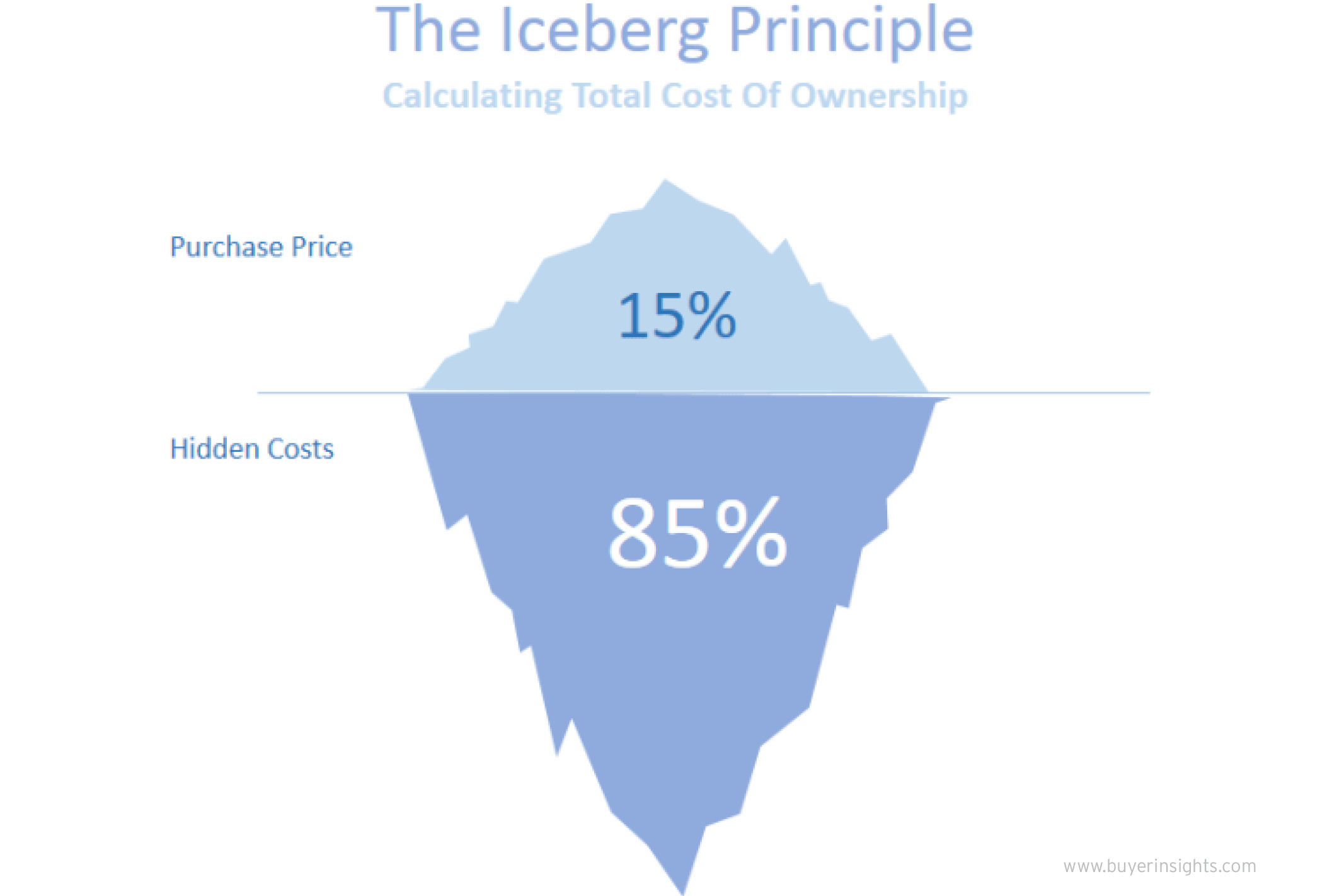
Material selection is one of the most important aspects of interior design. Beyond aesthetics, many factors go into the final decision, including code compliance, performance, and environmental and health impacts.
For building owners, cost is the driving factor behind the selection process. Although choosing inexpensive materials can lower construction costs, this decision can have long-term repercussions.
At Neumann Monson, life-cycle cost analyses are central to our process. We often tell clients that initial costs are only the tip of the iceberg. The true cost of building ownership occurs over the building’s lifetime.
Our goal is to help building owners lower long-term maintenance and replacement costs. This article will discuss life-cycle costs for interior materials and explain how spending a little more upfront can lower the long-term cost of building ownership.
What is a Life-Cycle Cost?
A life-cycle cost is the total cost of a building system or material over its lifetime. It includes the cost of acquiring, maintaining, replacing, and disposing of the system or material.
Like an iceberg, a material’s initial cost is the most obvious—but the hidden cost of maintenance and replacement lurks below the surface. Often, materials with a lower initial cost require more maintenance and need to be replaced more often. In the end, they will cost a building owner more than a durable option with a higher initial price.
Life-cycle costs apply to almost every material and system that goes into a building, especially those that face wear and tear from weather or occupant use. Projects that use public funding must undergo a life-cycle cost analysis for systems that impact building performance, including:
- Mechanical and HVAC systems
- Lighting systems
- Building thermal envelopment systems
- Domestic hot water systems
Typically, a third-party energy consultant performs a systems analysis. A life-cycle cost analysis for building materials is more informal and can be performed by an architect or interior designer.
A Case Study: VCT vs. Polished Concrete
To lower the long-term costs of building ownership, invest in the areas of the building that have the greatest impact on your operational budget. In commercial buildings, flooring is a crucial investment.
Floors go through plenty of wear and tear and require frequent maintenance. Durable flooring options tend to have a lower life-cycle cost.
Let’s look at a real-world example. Recently, a commercial client needed a new prototype store to implement across their portfolio of properties. When they approached us, they had over 60 stores across four states that used Vinyl Composite Tile (VCT) flooring.
Although VCT has a low initial cost, it requires frequent waxing and stripping. It also needs to be replaced once every ten years, depending on foot traffic. These expenses increased the client’s operational budget greatly.
The new prototype store used polished concrete. Unlike VCT, polished concrete is low maintenance, making it ideal for a retail environment with regular foot traffic. Rather than waxing, it can be cleaned with a mop. It can also last over 40 years.
Although polished concrete had a higher initial price tag than VCT, the client received a return on investment through decreased maintenance and replacement costs.
Life-Cycle Costs for Other Flooring Materials
Often, flooring materials with the highest initial cost offer the lowest life-cycle costs. The following graphic breaks down the initial and maintenance cost of different flooring options.
Life-cycle costs of flooring options.
The materials with the highest initial cost tend to be low-maintenance and the most durable.
Porcelain Tile, for example, is one of the most expensive flooring options, but it requires little maintenance and can last decades.
Materials with a lower initial cost, like VCT and Sheet Vinyl, need the most maintenance. They also need to be replaced at least once in a 20-year cycle. Carpet Tile is lower maintenance but needs to be replaced as often as VCT or Vinyl Sheet.
These frequent replacements can add up over time, and you may pay more than you would have by choosing a more durable material upfront. Depending on your organization, replacements can also impact operations and result in lost revenue.
Learn More About Material Selection
The cost of a building extends well beyond construction. To lower your operational budget, analyze the life-cycle costs for the materials and systems.
While a third-party energy consultant will perform a life-cycle cost analysis, an architect or interior designer can help you analyze the long-term cost of materials.
Even with a limited budget, it is important to invest in materials that face the most wear and tear and have the greatest impact on your operational budget. For many commercial building owners, flooring is the greatest concern. Your architect should guide you through the material selection process and help you achieve a durable interior that saves you money in the long run.
Maintenance and replacements are only some of the factors to consider when selecting materials. It is also important to set goals for occupant health and sustainability. Learn more by reading about the material selection process.