Encouraging Transparency: LBC Materials Petal at the Stanley Center
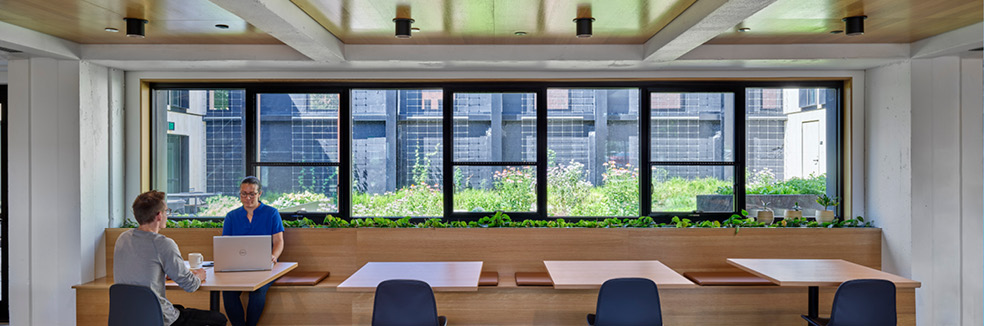
Recent research has linked building materials to many adverse environmental issues. In addition to pollution and resource depletion, many common materials can cause negative human health impacts.
Realigning how we select materials and advocating for more sustainable options has become a priority for the design profession. One pathway is the Living Building Challenge (LBC), a third-party building certification system.
Its Materials Petal focuses on the products used to construct buildings, their ingredients, and sourcing. It also promotes material reuse and recycling to minimize waste.
In Muscatine, Iowa, the Stanley Center for Peace and Security is on its way to becoming the second renovation to receive a full LBC certification. To celebrate this achievement, we are discussing how the project fulfills each LBC Petal.
This article will focus on the Materials Petal and how the Stanley Center meets its requirements.
Understanding the Materials Petal
The Living Building Challenge is the most holistic and rigorous approach to sustainable design. Its framework is broken into seven categories known as Petals, which include:
- Place
- Water
- Energy
- Health and Happiness
- Materials
- Equity
- Beauty
The Materials Petal aims to create a non-toxic, transparent, and ecologically restorative materials economy. It seeks to remove chemicals known to harm human health and push the industry toward more responsible practices.
Of the seven LBC Petals, the Materials Petal can be the most challenging. The materials market has significant limitations, making it difficult to find healthy, sustainable products with transparent manufacturing processes.
As such, the LBC promotes advocacy. Design teams should communicate with product manufacturers, help them understand the importance of material transparency, and encourage more environmentally responsible practices.
The Materials Petal at the Stanley Center
Every LBC Petal contains separate requirements known as imperatives. The Materials Petal has five, including:
- Responsible Materials
- Red List
- Responsible Sourcing
- Living Economy Sourcing
- Net Positive Waste
The Responsible Materials imperative is a Core requirement, meaning any project seeking certification within the LBC program must achieve its standards. It specifies the use of Declare Label products, which the International Living Future Institute (ILFI) recognizes as aligning with LBC values. It also sets requirements for lumber use, local economy sourcing, and recycling.
By seeking a Full LBC Certification, the Stanley Center met the requirements of the Responsible Materials imperative plus the other four imperatives. Below, we’ll discuss these imperatives in greater detail.
Red List
The Red List outlines chemicals that are known to harm human health. Such chemicals can be found throughout buildings—from piping to finishes.
Chromium, for example, is a known carcinogen commonly found in paint. PVC, often used for piping and casework, is linked to respiratory irritation. Other chemicals, like Bisphenols (BPA), are found in plastics and sealants and can inhibit childhood development.
Fully certified LBC projects must avoid Red List chemicals in at least 90% of new materials by cost. Achieving this goal can be difficult, requiring extensive research into products and their ingredients.
To complete this research, we partnered with Integrated Eco Strategy, a consultant well-versed in the LBC. Their database contains the Living Future's catalog of Red List materials, as well as materials populated from other LBC projects. This tool helped vet potential products and find alternative options.
Rather than a centralized approach, we gave the construction team full access to the database. Nearly 50 people could access material information and partake in the vetting process.
This decentralized approach was uncommon, but it improved communication and efficiency. Everyone understood the project’s goals and the logic behind material selections, helping both the design and construction team vet options more quickly.
Responsible Sourcing
The Responsible Sourcing imperative supports sustainably extracted materials with transparent product labeling.
Projects must source at least 80% of all wood—by cost or volume—from a Forest Stewardship Council (FSC) certified manufacturer or use salvaged products. Other wood products must be from low-risk sources. Projects must also contain two Declare Label products for every 200 square meters of gross building area and encourage manufacturers to pursue the label.
At the Stanley Center, over 140 products have Declare Labels. HNI in Muscatine achieved labels for all systems-based furniture and office fronts included in the project.
Office front systems and furniture received Declare Labels.
When transparent labeling was unavailable, the design team sent advocacy letters. Over 1,700 letters were sent throughout the project, informing manufacturers of the importance of honest information sharing.
Living Economy Sourcing
The Living Economy imperative promotes locally made products to encourage economic growth and minimize the carbon emissions associated with transportation.
At least 20% of all materials by cost must come from within 500 kilometers of the construction site. 30% of material must come from within 100 kilometers, and an additional 25% must come from within 5000 kilometers. The remaining 25% of materials can come from any location.
The Stanley Center exceeded these expectations, with 50% of materials coming from within 500 kilometers. Major items like concrete, structural steel, roofing, and pavers were sourced locally. Interior materials—including wood veneers, acoustic baffles, and recycled glass countertops—also came from area manufacturers.
Oak veneers and acoustic baffles were sourced locally.
Whenever possible, the project team strove to work with the nearest manufacturers. For example, HVAC systems represent some of the highest costs associated with a commercial project.
Although the HVAC manufacturer was based in Canada, the team worked with its nearest distributor in Minnesota. This maneuver meant one of the most complex and labor-intensive portions of the project was closer to the site. In the end, only 9% of all materials came from beyond 5000 kilometers.
Net Positive Waste
Lastly, the Net Positive Waste imperative seeks to reduce waste and encourage reuse at all project phases. It sets requirements for recycling materials like steel, carpet, insulation, and demolition waste.
Design teams must consider product durability to minimize future waste and create a plan for recycling and reusing materials during construction.
At the Stanley Center, 95.2% of construction and demolition waste was diverted from the landfill. Recycling waste was challenging. Glass, for example, had to be broken to determine its recyclability—once over a FaceTime call with a glass recycler.
With recycling presenting challenges, the team strove to reuse as many materials as possible. Existing roof membranes were reused, and pavers were repurposed to support outdoor light fixtures.
As an adaptive reuse project, the building used fewer materials than new construction. Nearly 95% of the existing building mass was reused, reducing the project’s embodied carbon footprint by 2/3 compared to new construction.
Learn More About Building Materials
Building materials and their impact has become a growing concern in the design profession. Although some unhealthy materials have been phased out of the market, there is more work to be done.
The LBC provides one path forward—showing designers how to research products and advocate for more material transparency. At Neumann Monson, these requirements helped our team become more intentional with product specifications.
We have adopted the American Institute of Architects (AIA) Design & Materials Pledge and are working to update our master specifications with more sustainable options. Learn more by reading about the Materials Pledge and how we plan to implement its framework.