Solid Wood vs. Veneer vs. Plastic Laminate: Which is Right for You?
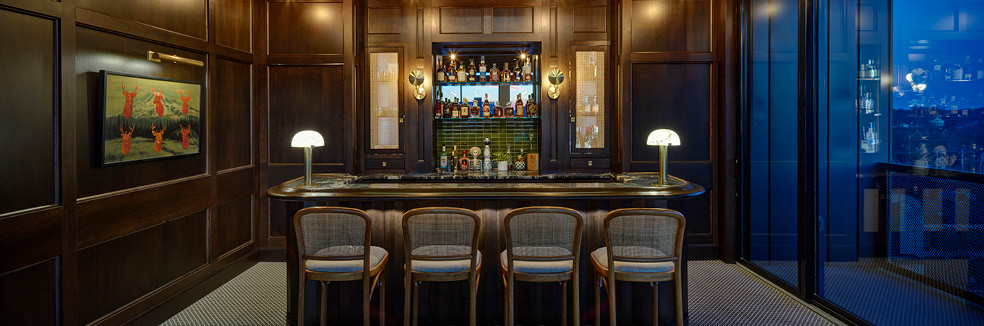
Selecting interior materials is a crucial part of the design and construction process. Choices have long-term implications, affecting aesthetics, maintenance, and life-cycle costs.
Typically, you will discuss interior materials during Design Development, with your design team walking you through your options. For projects with casework elements—like built-in cabinetry, bookshelves, or workstations—your design team will likely suggest solid wood, veneer, or plastic laminate.
Each material has pros and cons, and the right choice depends on your goals and the building’s function. To help you determine which is right for you, this article will discuss the differences between hardwood, veneer, and plastic laminate and the pros and cons of each option.
The Difference Between Solid Wood, Veneer, and Plastic Laminate
Solid wood, veneer, and plastic laminate are the three most common casework and furniture materials.
Solid wood refers to hardwood products, typically made from deciduous trees like oak, walnut, maple, and ash. Such trees grow slowly, giving them strength and durability.
Veneer, on the other hand, refers to engineered wood products like Medium Density Fiberboard (MDF) covered with a thin premium wood cover. While veneer products may resemble hardwood, they are lower on the cost spectrum.
Plastic laminate products are similar, with a laminate layer over MDF. With both veneer and plastic laminate, color and finish options are endless.
Pros and Cons of Solid Wood
Solid wood provides durability and longevity. It is difficult to scratch or damage, making them popular in residential settings. It also ages well, developing a patina over time. If owners wish to change the look, solid wood is easy to refinish.
Solid wood is the most natural of the three options. Unlike engineered wood products like MDF, solid wood contains no adhesives or chemicals, making it the best choice from a material health standpoint.
Despite its durability, solid wood does not fit every setting. Wood is likely to expand and contract as it responds to humidity. This expansion and contraction can lead to warping and cracking, depending on the situation. Owners choosing solid wood products should prepare for some level of imperfection.
Solid wood also tends to be more expensive than veneer or plastic laminate. While some wood types, like birch, are at the lower end of the cost spectrum, others, like walnut, tend to be more expensive.
In our experience, the cost of solid wood depends on sourcing. When renovating our Iowa City studio, we went through an urban lumber program to acquire ash hardwood. The lumber—produced from dead, dying, or diseased trees—came from within ten miles of the building site.
Using urban lumber can help reduce the cost of hardwood.
Compared to commercial hardwood, this lumber had a much lower price point. If you are considering solid wood, we recommend looking into urban lumber programs to potentially reduce the cost and utilize a valuable local resource.
Pros and Cons of Veneer
While providing the look of solid wood, veneer products are more dimensionally stable. They will not expand or contract and can maintain their look for years with proper care.
Veneer products work well for those who desire a natural look but want something more predictable than solid wood. They are found in residential and commercial buildings, including offices, schools, and hospitality settings.
While providing the look of hardwood, veneer products are less likely to warp.
Although veneer products are dimensionally stable, they do not offer the same durability as solid wood. Veneers cannot be refinished, and scratches may reveal the MDF substrate. However, compared to plastic laminate, damage to veneers tends to be less noticeable.
From a cost standpoint, veneer products fall in the middle. While they are lower in cost than solid wood, they tend to be more expensive than plastic laminate.
Pros and Cons of Plastic Laminate
Often, plastic laminate is used in settings where cleanability is a top priority, like healthcare and K-12 buildings. Unlike solid wood and veneer, it is easy to wipe down and can withstand chemical disinfectants, making it the ideal material for owners prioritizing infection control.
In addition to its cleanability, plastic laminate is affordable. It tends to be lowest on the cost spectrum compared to hardwood and veneer.
Easy to disinfect, plastic laminate works well for healthcare settings.
With proper care, laminate products can last decades. However, owners may experience problems with laminate in high-traffic areas. Edge banding can peel or chip over time, and unlike hardwood and veneer, damage is difficult to hide. While wood products develop a patina, plastic laminate can discolor over time.
Plastic laminate is also the least natural and least sustainable of the three options. The MDF substrate contains chemicals and adhesives, and when laminate reaches the end of its life cycle, it is likely to end up in a landfill. For some, cleanability and infection control may take precedence over these considerations.
Which Option Is Right for You?
When choosing between solid wood, veneer, and plastic laminate, the right choice depends on your building’s function and your long-term goals.
Some project types, like healthcare and K-12, must prioritize cleanability, making plastic laminate the most logical choice. Veneer and solid wood work well in situations where infection control is a lower priority.
While solid wood offers more durability and longevity, it can warp and crack depending on humidity levels. Those wanting a more predictable product may opt for veneer and the dimensional stability of MDF substrates.
Your choice also depends on your long-term goals and how long you plan to occupy the building. Solid wood can withstand more wear and can be refinished in the future. It is also the most sustainable choice, especially when using local lumber.
If you plan to occupy the building well into the future, it may make sense to invest in solid wood. An option with a lower initial cost—like veneer or plastic laminate—makes more sense if you are unsure how long you will occupy the building.
Ultimately, every project is unique, and the right choice depends on several factors. Your design team should guide decision-making and help you understand how your choice will impact your operations, maintenance, and life-cycle costs.
Life-cycle costs refer to the long-term cost of ownership—including the cost of maintenance, replacements, and cleaning. Every interior material has a life-cycle cost, which is why we recommend investing in areas that experience the most wear and tear. To learn more, read our article on the life-cycle cost of interior materials.